Products
Complete Solids Control offers high-performance centrifuges designed to efficiently remove ultra-fine solids from drilling fluids. Made with high-grade stainless steel for superior durability and corrosion resistance, our centrifuges optimize mud properties, reduce disposal volumes, and enhance overall drilling efficiency. Supported by skilled technicians, our equipment provides reliable, precise solids control to keep operations smooth, safe, and cost-effective.
Complete Solutions for Drilling Efficiency and Waste Reduction
At Complete Solids Control, we understand the unique challenges in drilling operations and are dedicated to providing solutions that tackle them head-on. Our range of advanced products, including centrifuges, drying shakers, and surface rentals, is designed to keep your operations smooth, efficient, and cost-effective.
Our Products, Your Solutions
At Complete Solids Control, our products are designed to solve the toughest challenges in drilling operations, enhancing efficiency and reducing waste every step of the way.
Centrifuges
How a Decanter Works
The centrifuge is fed through a stationary pipe inside a hollow shaft connected to the screw conveyor (scroll). The feed enters a compartment within the conveyor and is accelerated through feed slots into the bowl’s interior. Once inside, centrifugal forces accelerate the solids, which collect on the bowl’s inside diameter wall. Meanwhile, the liquid forms a concentric annulus and fills the bowl to the level of the effluent dam/weirs.
The screw conveyor, coupled to a gearbox, rotates slightly slower than the bowl. This slower rotation, combined with the helix angled toward the smaller diameter (conical end), conveys the solids along the bowl’s inside diameter to the solids discharge end.
The liquid flows around the screw conveyor and exits through the effluent dam/weirs located at the larger diameter (cylindrical end) of the bowl. Solids that do not settle on the bowl’s inside diameter (floaters) are carried out with the liquid through the effluent weirs.
Adjustable effluent dams/weirs control the liquid volume inside the bowl. The maximum volume (pool) creates an annulus diameter smaller than the solids discharge diameter, ensuring effective separation and discharge.
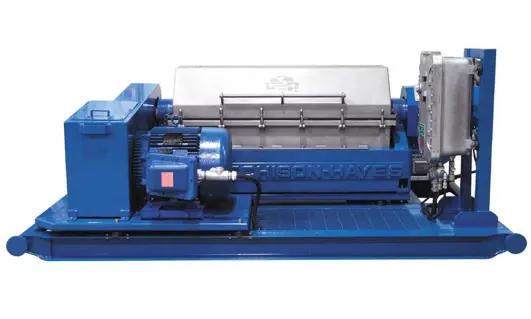
HH1448
Maximum Rated Capacity 225 GPM
Minimum temperature: 30F
Maximum temperature: 212F
Recommended throughput:
MUD weight 13 PPG: 30 GPM
MUD weight 11 PPG: 60 GPM
MUD weight 10 PPG: 100 GPM
Barite recovery RPM: <2250 RPM
Conveyor diffrential 42 RPM
G-force: 1000 G
Polishing RPM: 3250
Conveyor differential 61 RPM
G-force: 2100 G
Run up time: 5 minutes
Run down time: 15 minutes
Maximum RPM allowed: 4000 RPM
Bowl
Diameter: 14\”
Length: 48\”
Conical section: 10degree
Conveyor pitch:4\”
Gear Box
Ratio: 1:52
Torque: 22000 lbs
Shipping Data
Net weight: 4500 lbs
Gross weight: 5200 lbs
Volume: 128 cu. ft.
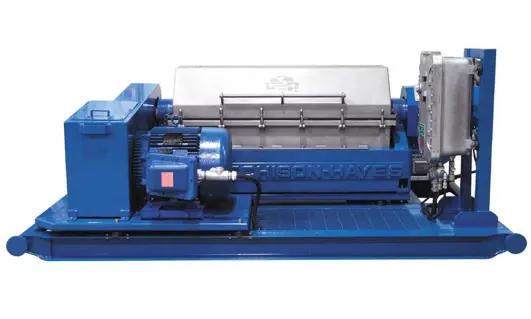
HH1448
The HH 5500 Standard is a basic drive system configuration for a decanting centrifuge. This setup represents the most fundamental option among various available configurations. The centrifuge bowl is powered by a main drive motor, while the conveyor is driven via a planetary gearbox with a simple torque arm arrangement.
The torque arm acts as a torque-limiting device, safeguarding both the gearbox and the conveyor from mechanical overload. The conveyor speed is determined by reducing the bowl RPM according to the gearbox ratio.
Maximum Hydraulic Capacity 230 GPM
Minimum temperature: 30F
Maximum temperature: 212F
RPM standard step sheave: 2,000 & 3,050 RPM
Run up time: 8 minutes
Run down time: 20 minutes
Materials
Bowl: AISI 316
Conveyor body: AISI 316
Base: Cast iron
Cover/Case: SS 316
Paint: Epoxy
Conveyor tips: Tungsten Carbide
Solids discharge: Tungsten Carbide
Feed nozzles: Tungsten Carbide
Bowl
Diameter: 16\”
Length: 55\”
Conical section: 10°
Conveyor pitch: 4.25\”
Gear box
Ratio: 53:1
Torque: 36,000 lb-f/in.
Shipping Data
Net weight: 8,200 Lbs
Electrical Requirements
Main Motor: 60 HP
Full Load Amps: 72 (460V, 3ph., 60Hz)
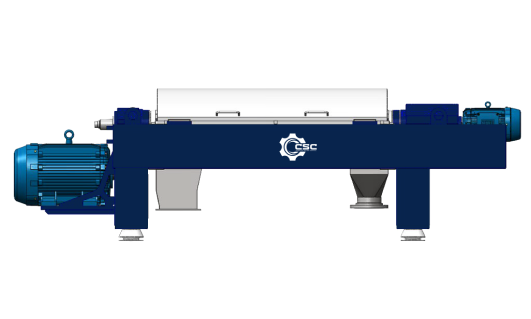
CSC18
Performance
Max Bowl Speed: 3,460 rpm
Rate Flow Capacity: 325 gpm
G-Force: 2246 G’s @ 3,000 rpm
Bowl
Diameter: 17.6” (447mm)
Length: 74.5” (1,892.3mm)
Beach Angle: 2.5° – 6° – 8.5°
Solids Discharge: 360°
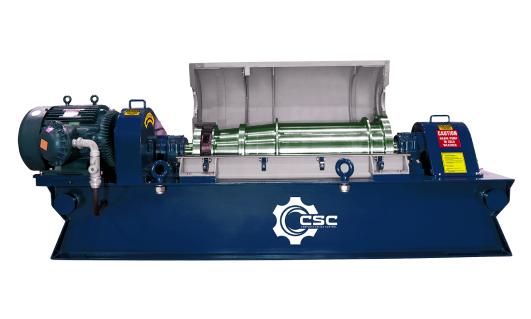
SS2000
Performance
Max Bowl Speed: 2,700 rpm
Max Centrifugal Force: 3,050 gpm
Rate Flow Capacity:660 Gal/Min
Unweighted Drilling Mud:528 gpm
Bowl
Material: Stainless Steel
Rotating Assembly: 21\”x72\”/125 hp (533 x 1829 mm)
Weight: 16,300 lbs (7,400 kg)
Beach Angle: 5°
Solids Discharge: 90°
Drying Shakers
Complete Solids Control offers premium linear motion drying shakers to ensure a fast and efficient turnaround time on your fluid recovery process. Our linear motion drying shakers are multi-functional drilling fluid cleaners built to handle varying drilling fluid viscosities and remove solids from drilling fluid.
Complete Solids Control and waste management services offer THE complete solution for closed-loop, zero-discharge systems. Our goal is to reduce liquid waste haul-off. Our linear motion drying shaker, coupled with advanced fine screening, plays a significant role in the complete closed-loop package. We can install double or triple shaker systems as needed.
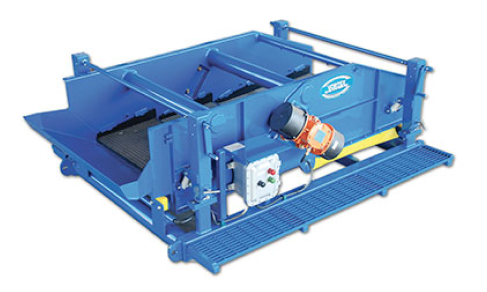
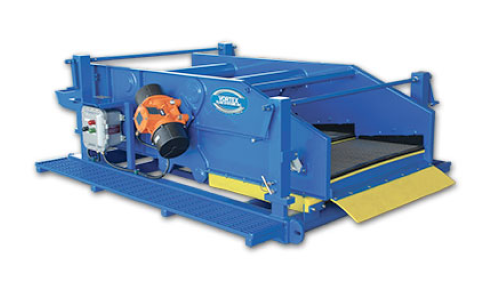
Orbital 3000 Drying Shaker With Walkways
DESCRIPTION
The ORBITAL® 3000 Drying Shaker with walkways is a four pannel shaker with extended feed section, mounted on an open frame base with personel walkways.
BENEFITS IN PROCESSING CUTTINGS
One advantage of the VFSI drying shaker is its ability to process cuttings efficiently. Competitor units feature stationary sections that funnel cuttings to the shaker. These areas are prone to clogging, require frequent clearing, and can cause a mess. The VFSI Orbital 3000 drying shaker, however, features an extended section that vibrates onto the screen, eliminating cuttings hold-up.
PERFORMANCE
The screen area of the Orbital 3000 Drying Shaker spans 30 ft² with 6 g’s of acceleration. The combination of screen surface area, high g’s, and screen motion makes the Orbital 3000 one of the best-performing machines in the industry. The Orbital 3000 shakers use progressive elliptical motion for extended screen life and excellent conveyance.
GRATED WALKWAYS
The grated walkways on each side of the unit keep the operator out of the mud and provide a convenient height to change screens and monitor performance.
FEATURES
ORBITAL® shakers have many beneficial features.
ACCELERATION: 6 g\’s (standard) to 7.5 g\’s (optional)
SCREEN AREA: 30 ft2 of screening area
MOTION: eliptical motion
SCREEN LIFE: ORBITAL® shakers have exceptional screen life
SEAL WELDED: Fully seal welded baskets.
LOW MAINTENANCE: Ultra low maintenance design
LOW NOISE: 70 db standing 3ft from discharge 10
ABRASION PERTECTION: two layers of powder coat
SCREEN SEALS: patent pending screen seals are as easy to change as a set of screens
VIBRATORS: vibrators are one of the most overbuilt electrically and mechanically in the industry
MANUFACTURING: Made in USA
Specifications
NAME: Orbital 3000 Sump Drying Shaker
SCREEN AREA: 30 ft2 [2.8 m2 ]
\”G\” FORCE: 6 g\’s (standard), 7.5 g\’s (optional)
MOTION: Progressive Eliptical
DIMENSION (LxWxH): 116×100-1/2×40-1/4in (295x255x102cm)
WEIGHT: 3200lb [1455 kg]
FEED HEIGHT: 25-3/8in [65cm] (standard) – adjustable
ADJUSTMENT ANGLE: 0 to 8 degrees
ANGLE CHANGE TYPE: hand crank (standard) or center wheel (optional)
SCREEN TYPE: pretension
SCREEN NUMBER: 4 screens
SCREEN SIZE: 48 x 24 in [112 x 61 cm]MOTORS: Italvebras, 1200 or 1800 rpm, 50 or 60 hz
MOTOR TYPE: explosion roof
ELECTRICAL BOX TYPE: explosion roof
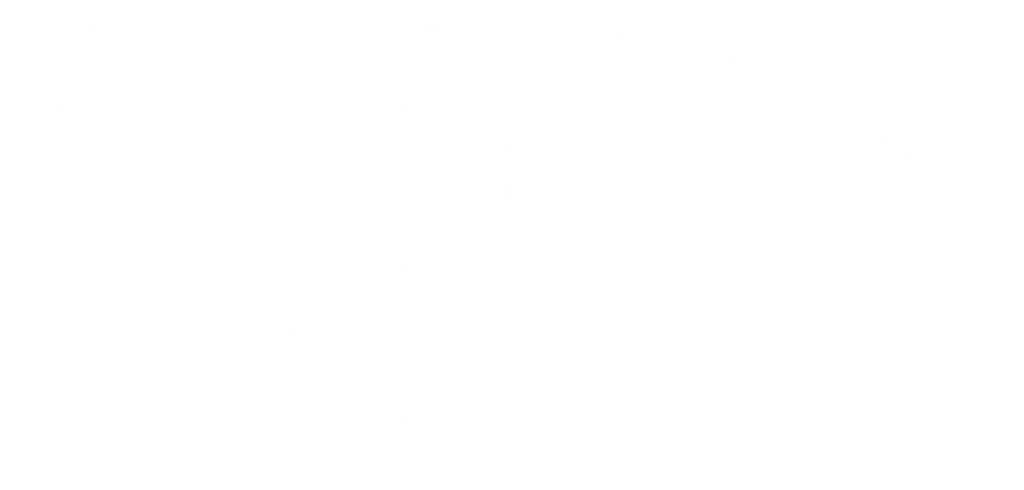
Surface Rentals
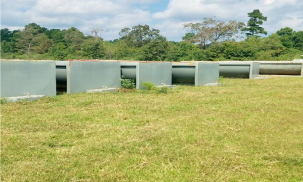
Open Top Containment
Our shale bins come in 20′, 30′, and 40′ L sizes, and are designed to fit any and all rigs for drill cuttings and solids handling. Built with heavy-duty industrial steel, these bins are engineered to prevent damage, making Complete Solids Control bins some of the most robust containment bins in the industry.
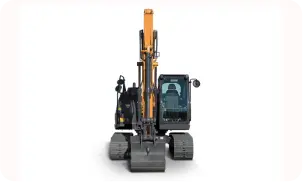
Case 130 Excavator
Our CASE CX130D excavators provide greater fuel efficiency, more power, higher lifting capacities, and better controllability. In addition to the high precision and smooth control of our CASE Intelligent Hydraulic System, the CX130D features a new electronically controlled hydraulic pump, a larger control valve, and solenoid valves. Operation is a breeze for solids handling and is managed by a Complete Solids Control experienced excavator operator.